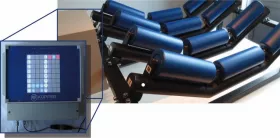
Users of belt conveyor systems, often with a length of several kilometres, want a user-friendly way to monitor important condition parameters of carrying idlers. Checking bearing temperatures is the leading aspect here since this is an important indicator for a pending bearing failure. If bearing damage is not identified in time, it leads to failure of the carrying idler or even damage to the transported material. Overheating of the roller bearing can cause damage to the conveying system and possibly catch the conveyor belt on fire.
The company Artur Küpper offers a preventive monitoring system to alleviate these hazards. It consists of a network of communicating carrying idlers that continuously delivers messages about the condition of the carrying idler components to the user, reports potential risks in a timely manner, and thus effectively prevents unplanned downtime.
A temperature-based sensor system with local measurement of the temperature in the vicinity of the bearing was designed for this purpose. Measurement with digital temperature sensors is not only technically suitable but also constitutes a solution of economic interest – compared for example to costly infrared and vibration-based systems.
The current evolutionary stage of development therefore encompasses the complete integration of the sensor into the carrying idler axle, including electrical contacting by means of plug contacts to the outgoing sensor lines on the carrying idler station. An integrated contact consisting of female and male pressure pieces was chosen for this purpose. Signal transmission is ensured by a pressure load on two brass pins that are compressed.
To install the female contact piece in the carrying idler axle, a form-fitting slot is milled perpendicular to the spanner flat. The contact piece is glued into this so it cannot be lost (Fig. 2).
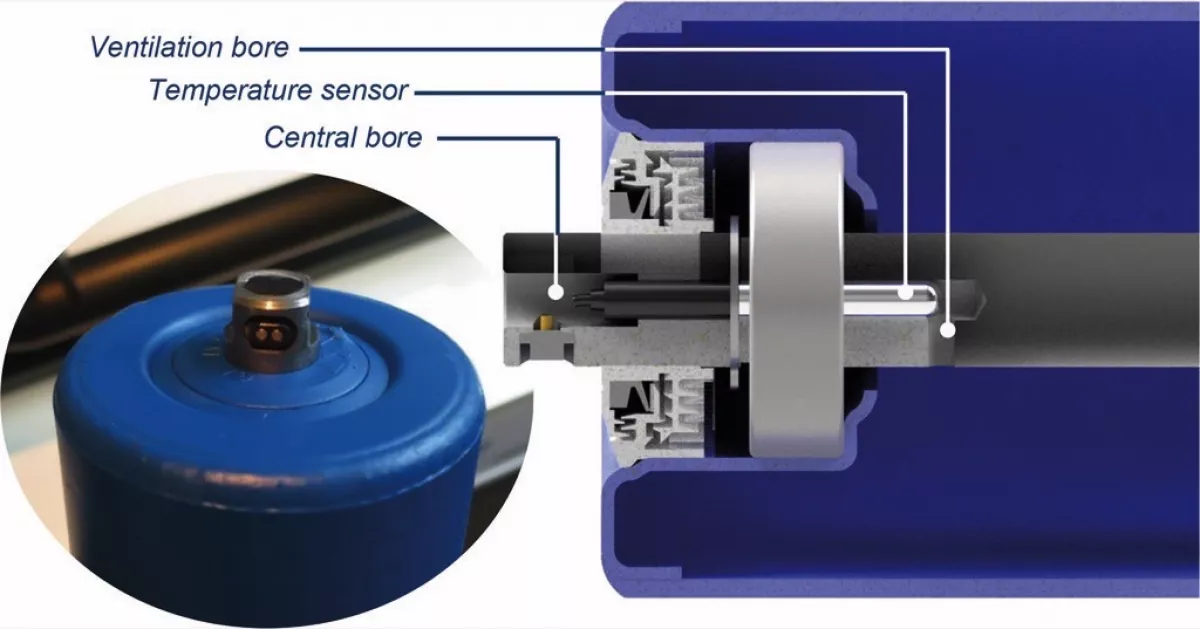
Implementing two temperature sensors per carrying idler results in the number per station, with 6 sensors that have to be administered. The states of these sensors are monitored with the AKT monitoring system, and evaluated and visualised on an RGB LED matrix. By means of the display, the actual position of the carrying idler can be determined within the conveying system and within the station (Fig. 3).
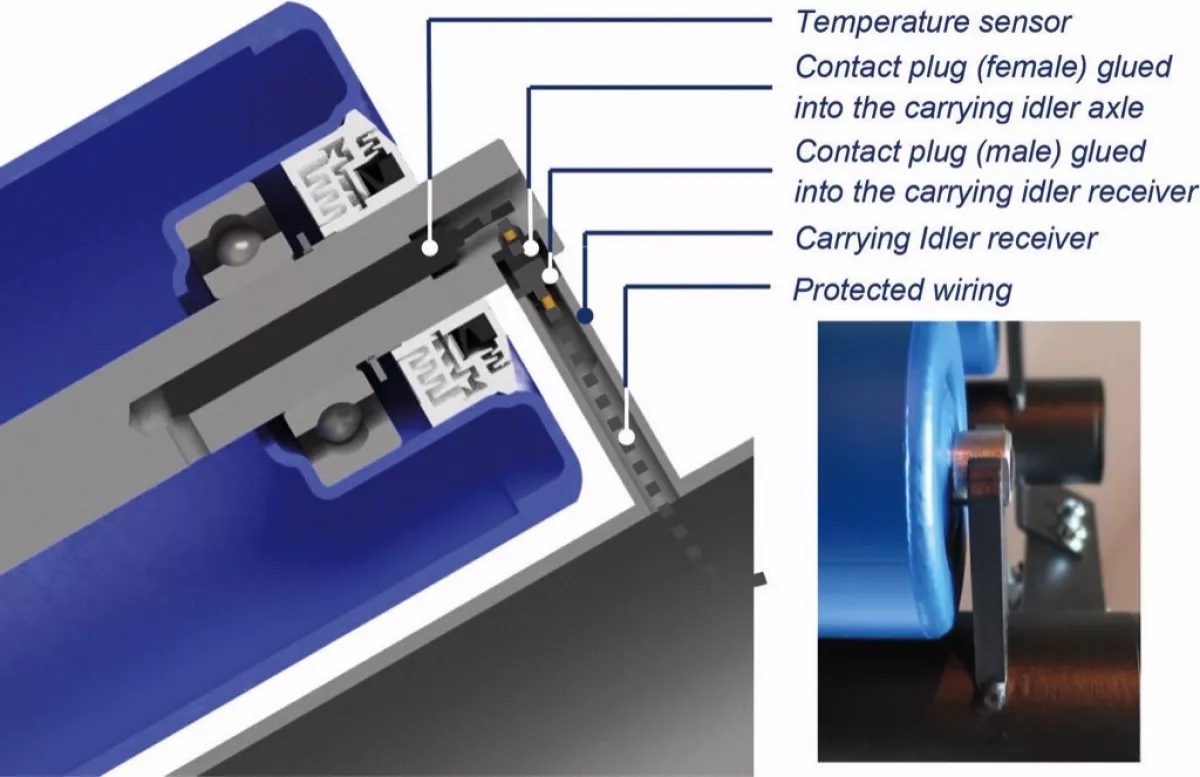
An appropriate measuring strategy is employed for the reliable evaluation of the sensor signals. The average temperature over a collective with a maximum of 16 stations is formed for this purpose. This ensures that the measurement is taken independently of the respective outside temperature and even different loads. An allowable excess temperature is defined depending on the location and conditions of use, and the critical temperature is calculated as an additional parameter with the arithmetical collective temperature. When the average collective temperature in turn is compared to the critical temperature, a statement about non-permissible temperature increases due to roller bearing damage can be made even in the initial stage.
The sensing idler system in development will be able to specifically detect roller bearing damage early on and, via the AKT monitoring system, provide direct feedback for a collective of up to 16 carrying idler stations per monitoring unit. This reduces the labour-intensive inspection of conveying systems to a minimum. Unplanned system downtime is prevented through the early detection of bearing damage on carrying idlers. Damage to the entire system due to overheating bearings or blocking rollers is avoided.
In princi
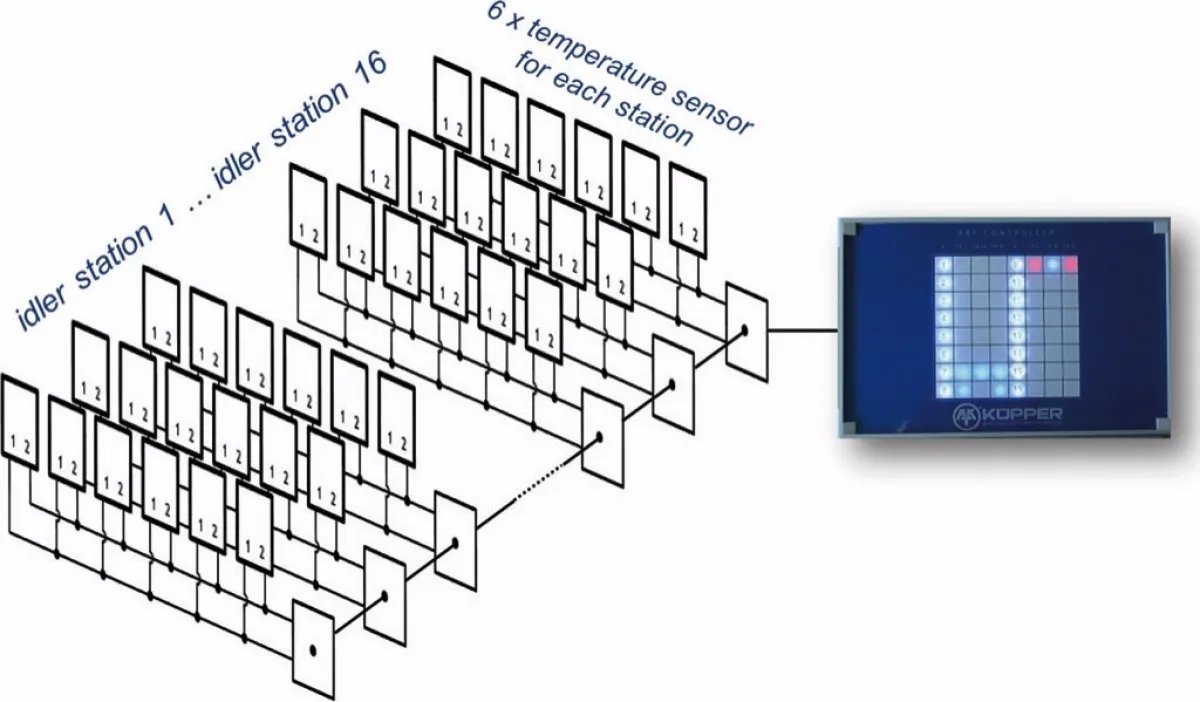
ple the application of the technology is universal. However, it is particularly meaningful where critical conveying systems with no redundancy are used. A conveying system for loading ships is an example. Its failure affects all connected conveying and logistics processes and is therefore very costly.
Acknowledgement
This article is based on a presentation of the authors during Schüttgutfördertechnik - Marktplatz für Innovationen, 27./28. September 2017 in Magdeburg, Germany.
■